- Kenmore refrigerator water filters
- Whirlpool refrigerator water filters
- Samsung refrigerator water filters
- GE refrigerator water filters
- LG refrigerator water filters
- Frigidaire refrigerator water filters
- KitchenAid refrigerator water filters
- Maytag refrigerator water filters
- Kenmore Elite refrigerator water filters
- Estate refrigerator water filters
- GE Profile refrigerator water filters
- Amana refrigerator water filters
- Bosch refrigerator water filters
- Dacor refrigerator water filters
- Electrolux refrigerator water filters
How to maintain an oil-lubricated air compressor
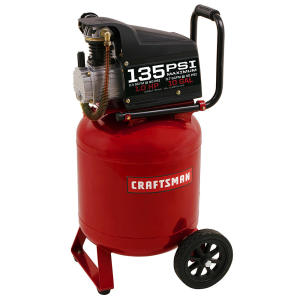
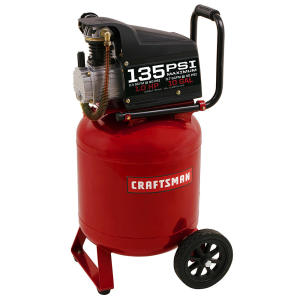
An air compressor is for more than just inflating tires–the energy contained in compressed air powers our most useful shop tools. Routine and regular oil-lubricated air compressor maintenance protects the investment made in an air compressor and ensures it works efficiently and safely.
Before each use, check the compressor hoses for any signs of wear. Inspect the tank for weak spots, pinholes and rust; if you find damage, replace the tank. Also, check the belt for any wear or damage and replace if needed.
Start the compressor following the instructions in the owner's manual, and once it reaches shut-off pressure, test the safety valve. Wearing safety goggles, pull the valve ring to release pressure from the tank. The valve should close automatically. If it doesn’t close automatically, or if it doesn't release air when pulled, replace the valve.
Test for air leaks by checking that all connections on the hoses, transfer tubes or pipe connections are tight. If you find a leak, replace the faulty component. Don’t over tighten any connections.
After each use, shut off the compressor, unplug it and bleed all pressure from the system. Drain the tank by completely opening the drain valve at the bottom. Check the pump oil level following the instructions in the owner's manual and add oil as needed. Inspect and clean the intake vents, and check the air filter, replacing it if worn or clogged.
For every 100 hours of use–or as recommended in your owner's manual–change the pump oil. This is also a good time to check the belt tension and pulley alignment. Check and tighten the bolts on the air compressor, being careful not to over tighten.
Most common symptoms to help you fix your air compressors
Choose a symptom to see related air compressor repairs.
Main causes: loose air tube fitting connections, bad check valve, faulty safety valve, damaged or corroded air tank, bad…
Main cause: bad check valve…
Main causes: tank drain valve open or leaking air, leaky air tank, bad safety valve, worn pump seals, bad pump valve pla…
Main causes: rusted air tank, loose air tube fitting connections, bad check valve, leaky safety valve, bad tank drain va…
Main causes: bad safety valve, pressure switch failure…
Main cause: faulty output air pressure regulator…
Main cause: bad air tank pressure gauge…
Main causes: lack of electrical power, check valve failure, bad pressure switch…
Most common repair guides to help fix your air compressors
These step-by-step repair guides will help you safely fix what’s broken on your air compressor.
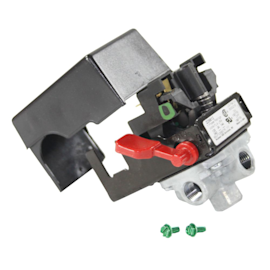
How to replace an air compressor pressure switch
You can replace a broken air compressor pressure switch in about 45 minutes. …
Repair difficulty
Time required
45 minutes or less
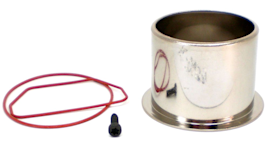
How to rebuild an air compressor pump
If the air compressor won't fill the tank with compressed air, rebuild the pump using these steps in about 45 minutes. …
Repair difficulty
Time required
45 minutes or less
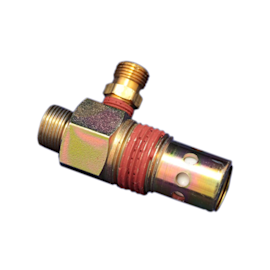
How to replace an air compressor check valve
You can replace a defective air compressor check valve in about 10 minutes.…
Repair difficulty
Time required
15 minutes or less
Effective articles & videos to help repair your air compressors
Use the advice and tips in these articles and videos to get the most out of your air compressor.
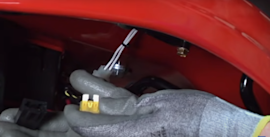
Learn how to tell whether a fuse is blown…
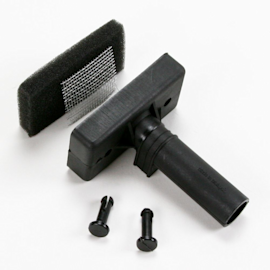
Find out how to reduce air compressor noise.…
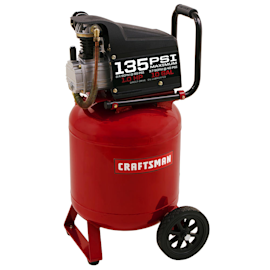
See how to perform routine maintenance on your oil-lubricated air compressor.…